Automation and flexibility may be key to future
Changing the job is likely to be an important factor in attracting and retaining staff, Anne Lee writes.
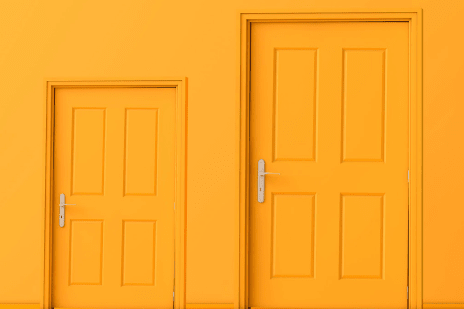
Changing the job to make it more appealing may mean investing in more automation in the farm dairy, having flexible milking times such as 10 milkings in seven days, or it could mean a complete rethink, extending lactation and only calving half the herd each year.
DairyNZ senior scientist Callum Eastwood says putting effort into thinking about this now is going to pay dividends as attracting and retaining a workforce becomes even more competitive in the near future.
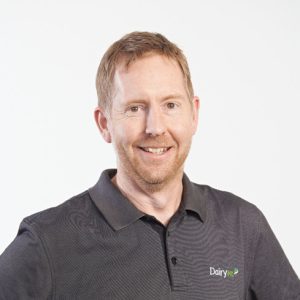
Not only will there be fewer people available, what those people want and how they view work is changing.
The ‘Change the Job’ aspect of the dairy sector’s Great Futures Dairying Plan is to find ways to:
- Reduce total and unsociable hours worked.
- Make the job easier, safer and less physical.
- Meet future workplace expectations.
- Increase productivity through better engagement.
- Improve flexibility of the workplace offering.
DairyNZ surveys found up to 60% of the work day is spent milking on some farms so strategies or investment in technology that reduces milking times can go a long way to decreasing work hours and relieving pressure.
Technology such as automatic cup removers (ACRs), auto teat sprayers and automatic drafting can reduce the workload at milking time and potentially remove a person from the farm dairy, particularly in rotaries.
Automatic plant and yard wash can also cut time spent in and around milking.
Using proven techniques such as MaxT or FixedT will cut milking times too.
Bigger system changes such as 10-in-7 regimes, 3-in2, and once-a-day milking could be considered.
Callum says results from DairyNZ’s latest technology survey show a significant uptake of in-dairy automation technologies when compared with 2018 data. (see table one.)
Working long and “unsociable” hours can be a turn-off for potential staff and be part of the reason people leave a job or even the sector.
Data from 2018 found just over half of people surveyed started milking before 5.30am and 30% finished after 5.30pm.
DairyNZ is working with farm teams at Pāmu on a study to gather more data on just how much sleep people get at various times over the season.
“The earlier you have to get up, the more difficult it is to get enough sleep unless you’re able to get into bed earlier too.”
For people with families or other responsibilities that can all be a big juggle. Unsociable hours can occur at either end of the day with people finishing late then not having enough time to wind down, eat well or carry out what they need to at home before having to get up again for the next early morning.
DairyNZ is also carrying out a study on 150 farms throughout New Zealand assessing productivity factors across the peak of calving, peak of mating, mid-lactation and the dryoff period.
“We’ve been working with QCONZ to gather the data which will give us good insights into productivity and allow us to get appropriate metrics we can then use to produce workplace productivity benchmarks.
“The information will help us build a picture of how many hours it takes to run a farm and carry out specific tasks that will help create benchmarks farmers will find useful.
“We have a lot of data from the survey including whether they have a rotary or herringbone shed, the topography, the quality of infrastructure, milking frequency and a big range of other information.”
When compared on a cows per full time equivalent (FTE) basis NZ ranks number one and is almost twice as efficient as the United States – largely because of their intensive indoor feeding systems.
But if the metric is kg milksolids (MS) produced per hour worked, the US is more efficient due to the high per-cow milk production.
“This data shows that focusing on cows/FTE alone could unintentionally drive the wrong behaviour with people put under too much pressure, however focusing on kg MS/hour could mask profitability factors.”
Milking productivity data shows the top 25% of farmers with rotary platforms milk 271 cows/person/day at peak and 67% of them have labour-saving technologies.
The top 25% of farmers with herringbone dairies milk 131 cows/person/day at peak with half having labour-saving technologies.
“What we need to look at, though, are a range of metrics – such as kg MS/hour, total hours worked per year or the number of unsociable hours worked per year and milking hours/total hours worked.
“If we can get good benchmarks on those, farmers can see how they compare and it will help drive better outcomes for them and for their staff.
Reducing total and unsociable work hours, making the job easier so it’s less physical and risky in terms of injuries all help to improve work conditions, he says.
Callum says DairyNZ is also working with 10 farms – five in Waikato and five in Canterbury – assessing workplace productivity and looking at ways to make efficiency changes using some aspects of Lean management and the Farm Tune programme.
“We’re learning from them and they are learning from each other, visiting each other’s farms and looking at how some aspects of the programme could be used to make a difference without going through the whole programme.”
Kanban practices to manage work flows or the use of software such as Trello can create efficiencies and improve communication onfarm so everyone knows what their tasks are.
“Those systems give people a level of autonomy too so they get to choose tasks.
“If we can change our jobs by reducing hours through efficiencies or technology then we can improve engagement and people are more likely to view dairying as an option and those who are already working in the sector will be more likely to stay longer.”
Links:
Kanban: www.dairynz.co.nz/people/managing-your-team/team-meetings/kanban-boards
Farm Tune www.dairynz.co.nz/business/farmtune
Milking efficiency www.dairynz.co.nz/milking/milking-efficiently