Switching off the 5am alarm is the dream of many dairy farmers. The Gemmells tell Cheyenne Stein how they have future-proofed their farm with the installation of their Lely Robotic milking shed.
For someone who is self-confessed computer-phobic installing a robotic milking shed doesn’t seem the best idea. But for Greg Gemmell and his wife Amy it’s been an idea they are glad they made and not just because they got to turn off the alarm.
Greg and Amy are sharemilkers on a farm owned by Amy’s parents, Brian and Margaret Schnell. Until last season the dairy had been home to a herringbone but after what they say was a bit of a joke about robots, they took the plunge and installed milking robots in its place. The couple, along with Amy’s parents each contributed to the costs of the installation.
The three Lely robots in the shed, which can milk about 80 cows up to three times a day in a 24-hour period, cost about $260,000 each, inclusive of all the automatic gates and software. The estimated running cost sits about $6000 a year which covers consumables and servicing, Steve Bromley, director and working manager for Bromley Dairy and Pumps who service the robotic system for the Gemmells, says. The first service is done after 20,000 milkings, then again at various intervals, just like a car, to ensure the system is running efficiently.
“We wanted to gain a bit of work-life balance as well as future-proofing the business. The herringbone needed an upgrade anyway and we figured if we could make it work on a low pay-out then it was worth a stab,” Amy says.
From start to finish it took 60 days for the dairy to be retrofitted for the robots. The Schnells and Gemmells did much of the groundwork themselves which saved money.
“It was a big gamble. We are still very much new to this and still figuring it all out. I haven’t had much time for computers so it has been a big thing for me to trust technology and stop thinking if I push a button I will break it.”
If issues do arise with the system, Lely are there to help with an on-call technician.
“I will never turn up to a yard full of cows that aren’t being milked. There will always be an alert to tell me as soon as there’s a problem. To date we haven’t had many, only after the earthquake, the system doesn’t like glitches in power, all we had to do was restart everything,” Greg says.
Although they are still in their first year they are happy with the results so far but say that every day is a learning curve and the massive amount of technology doesn’t mean they can stop being good farmers.
“You still have to be a good farmer. The computer system is pretty good at picking up things like when a cow is in heat, but you still need to be double checking for false heats and managing the pasture and animal health,” Greg says.
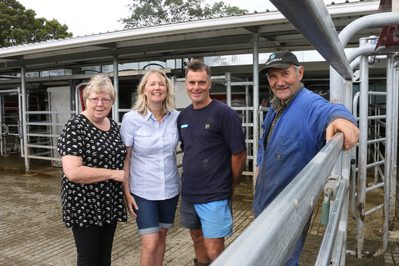
Fitbits for cows
As part of the robotic milking system, cows are fitted with a collar which has multiple functions, a sort of Fitbit for cows. Acting also as a visual identifier, the responder attached to the collar communicates with the milking robot for things such as robot acceptance.
If a cow tries to enter the pre-milk area, which guides her into a robot, sooner than her allocated hours after her previous milking, the gates will open for her to enter the post-milking area and then back out to pasture, so she won’t have acceptance into the robot at that time.
The collars also collect information such as steps taken, rumination and heart rate. This information is sent back to the system’s computer to store. A picture of her normal activity is created and deviations are picked up through algorithms to determine key events going on in a cow such as heat.
Ruminations are picked up via sound waves. A cow normally has 400 ruminations in a 24 hour period. When a cow is coming into heat, the number of ruminations decreases and the steps she takes in a day will often increase. These changes are picked up and shown as a report. She will also be automatically diverted off to a draft area if this option is set up. The system is more sophisticated than just reporting, though. Greg is able to track how far through a heat a cow is by looking on his computer and a progression bar will tell him when the optimum time for insemination is.
“The system is pretty good but you still have to be a switched-on farmer. Some days the system could say you need to put 40-50 up for insemination, but in reality they might not all be in heat. Flies might have annoyed them or a stray dog in the paddock has got them moving .There are a number of factors that could trigger the algorithm so you still have to be able to detect heat and double check otherwise it can end up costly.”
A new add-on to their system will hopefully mean a trouble free calving this year. The add-on, which is able to detect when a cow is in distress, works through an antenna on the roof of the dairy. When a cow comes within the 500-metre range the data picked up from her collar is compared to that of her peers. If her data is drastically different to her peers, an alert via a phone app will be sent to let Greg know there’s something not right with the cow.
The timing couldn’t be more perfect with heifers in calf to low-birthweight, pedigree Hereford bulls coming on now. Greg will keep this calving mob within range in case any issues arise from the slightly larger calves. Greg held his spring heifers over to calve in autumn for more maturity to help with calving but also so they would be larger when training in the robot to fill out the box and to kick-start their new autumn herd.
Animal health and environmental benefits
One of the biggest selling points of robotic milkers is the benefit in animal health. With the robots continually sending information into the computer at every milking, seemingly very little will go unnoticed.
“One thing we have noticed is that when there is a lot of people around cell count can be elevated. When there’s no-one around, it’s very different and that’s something we hadn’t really picked up on before,” Greg says.
“A cow isn’t meant to be moving fast, getting pushed into the shed or even pushed along by the herd at a pace she isn’t comfortable with and getting stressed. Now that they can walk in when they please we are finding lameness isn’t an issue.”
When somatic cell count spikes or mastitis is recognised the Gemmells have found they aren’t as quick to treat with antibiotics. Pre-robot days as soon as he saw clotting Greg says he would rush in and treat it, but they have learnt over time that given a few days, most cows come right on their own.
Now they wait a few days, use homeopathic sprays and allow the cows to come in when they want to be milked.
“They generally come right within a few days and instead of their milk being diverted to the calf milk area for weeks after antibiotics it’s only for a few days.”
By January most years they would have treated up to 50 cows already, but this year they have only had to treat three, and looking back they say they possibly rushed into that.
“Having that information at every milking makes us feel more comfortable with not rushing into treatment because we can see them getting better.”
Effluent, or lack of it, has also been a big advantage. The cows are leaving more effluent in the paddocks rather than the shed meaning built up soil fertility in the pasture and less cleaning to do in the shed, saving water and time.
“We are using a biological fertiliser system without urea and also think this has been helpful with cow health stemming from the soil and pasture health.”
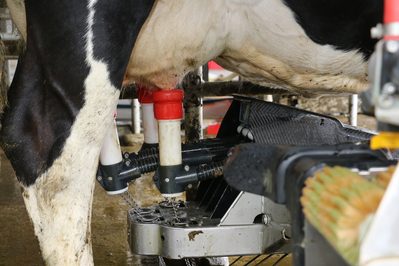
Cow behaviour and training
The dairy is open 24 hours a day for cows to wander in and out of at liberty but even six months down the road, the cows still maintain their herd mentality which the Gemmells say it will take a year or two for them to lose.
“With the robotic milking they can be an individual cow, but they are still trying to act as a herd. You get one cow wander up to the dairy and there’s usually a group behind her. It takes them a while to figure out they can come up anytime.”
The first time cows go through the system is labour-intensive and the scene looked like the country version of a rugby scrum, similar to teaching cows to walk on to a rotary.
“We had to make up training gates for them and drive them into a robot box like a rugby scrum. It took three people – one to console her, one programming the co-ordinates to set cups to teats and one helping push her in,” Greg says.
Once in the robot there are a number of pre-milking treatments like teat brushing to get rid of bacteria and stimulate milk let down. These were turned off the first time cows entered the robot and were gradually switched on to acclimatise them.
As with most animals, once they saw the food, the cows were more than willing to walk into the robot.
The voluntary milking system means cows can come and go as they please. Peak milking times have moved from 5am and 3pm, to 7am and 4pm with many coming through the middle of the night for a third milking.
“I reckon the cows are telling us they didn’t want to be woken up at 5am, just like we didn’t want to get up that early,” Greg jokes.
The herd is not strictly twice-a-day or once-a-day, they have a mix of once, twice and three-times-a-day milkers. If a cow is light in condition they can plug in her collar number and set up the programme to only accept her for milking once a day.
Nearly a year into their new venture the Gemmells are pleased with the results and are confident they made the right decision. Despite all the positives, Greg says he does sometimes feel guilty for his 7.30am sleep-ins.
Footnote: The Gemmells have had a number of visitors and tours through their robotic farm.
To arrange a tour email them at robotfarmnz@gmail.com.