‘Hands solo’ for cow collar farmer
Pirongia dairy farmer Fraser Hasnip recently went to Waiheke for the weekend and was able to shift cows from his phone using virtual fencing technology.
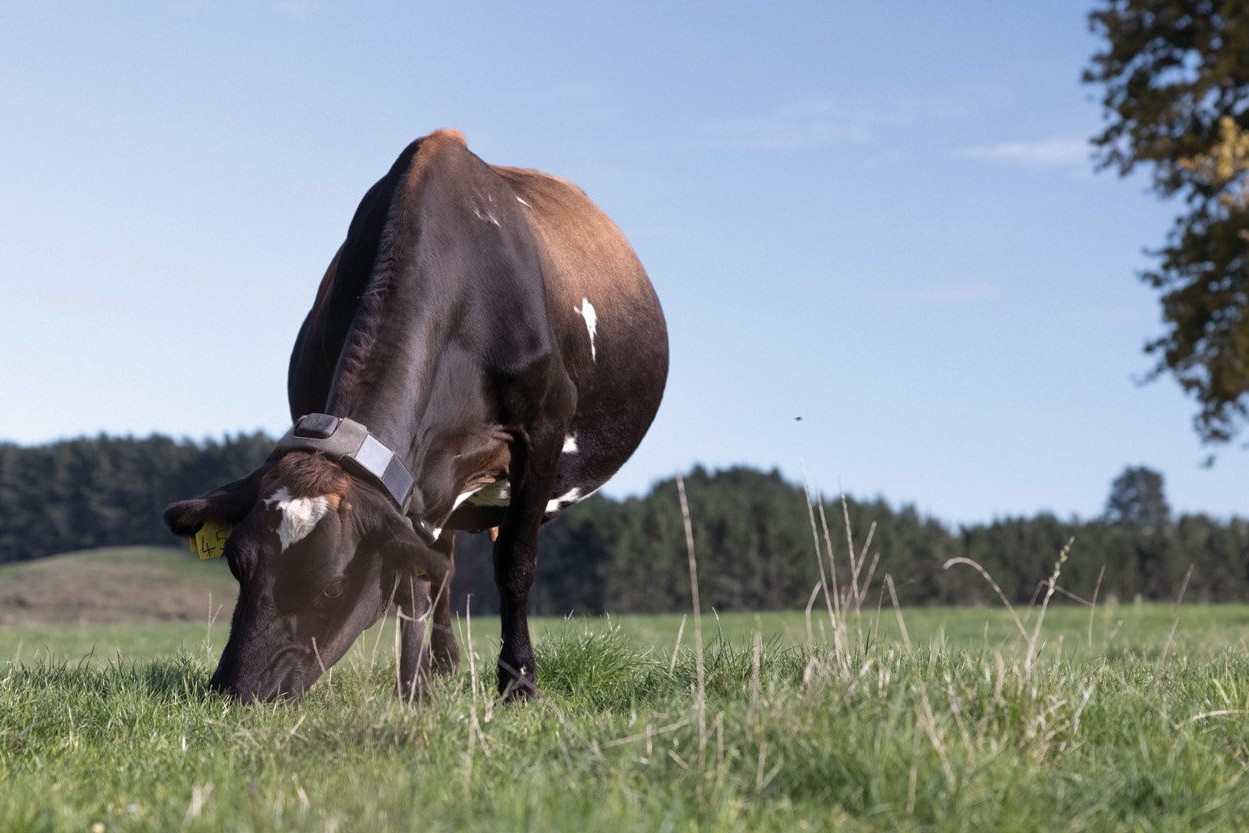
Fraser Hasnip recently went to Waiheke for the weekend and was able to shift cows from his phone using virtual fencing technology. The smart cow collars have been a game changer and are allowing him to run his 300-cow farm solo, even during calving. He talked to Sheryl Haitana about how Halter is changing his future in farming. Photos: Emma McCarthy.
Fraser Hasnip used to lay in bed listening to the rain getting heavier before making the decision to get up, put his wet weather gear on and go shift the cows off the paddock. It’s an all too familiar story most dairy farmers have experienced at some point to prevent pasture pugging.
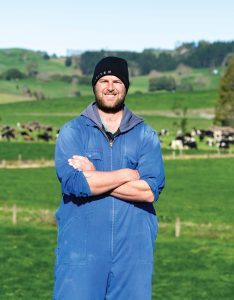
Now, Fraser can simply push a button on his phone, roll over and go back to sleep, and the cows shift themselves.
It’s just one of the labour savings Halter has created.
No more lugging around reels and standards, putting up break fences. No sitting on a motorbike following cows to the farm dairy or locking them away. Drafting springer cows out of the dry mob is no longer a game of bullrush with a break fence in a paddock. In fact it requires no hands-on effort.
“It’s been game changing. it has given us back a lot more time to run the farm so I can run it as a one-man operation,” Fraser says.
Fraser’s parents Peter and Sue Hasnip own the 106ha of easy rolling country under the Pirongia mountain in the Waikato. Fraser lives onfarm with his wife Claire and two children, a third on the way, and manages the 300 Friesian crossbred cows.
Recently on a family weekend away to Waiheke to celebrate Sue’s birthday, Fraser was able to schedule times for the cows to shift to the next break back at the farm.
He could see every cow live on his phone at any time. to know where they were and if they were okay.
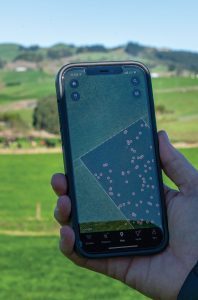
“I did think I might be looking at the cows all the time on the phone, but I don’t. It’s given me confidence that the cows are in the right place and the cows are okay, and given me comfort when we are away.”
In future, if Fraser employs a relief milker, he can schedule the cows to be moved and to come to and from the farm dairy. All the relief milker has to do is make sure the gates to the right race are open.
It was Peter who initially grabbed a pamphlet from The National Fieldays when Halter was in the Innovations tent and Fraser registered his interest. The Halter team put the collars on the cows last September and Fraser has been working closely with the team giving feedback on how the collars are working on the farm, as the company rolls out commercially.
VIRTUAL FENCE TECHNOLOGY
The collars work by making a sound to alert the cow they are nearing a boundary or ‘virtual fence’.
When the collar vibrates it signals to the cows that the boundary has been removed and they can move to fresh grass.
If they go past the boundary they get an electric pulse. The pulse is only needed in the first few days, the cows then respond just to the sound and vibration in the collar.
It took the cows just days to be trained to respond to the collars, Fraser says.
“The cows are extremely smart, they learnt the virtual fence in two days. I used to be their signal, or the bike, that they were going to be shifted. Now they know the collar is their signal – they learn to trust the collar. They turn on the sound beautifully. It’s like they have a little shepherd on their shoulder.
“I also haven’t had an electric shock for 10 months.”
Fraser immediately saw how successful the cows were staying within the virtual boundaries and started taking down fences to allow easier pasture management.
“Ironically, I spent lockdown doing fencing. We’ve slowly been taking down fences, they’re an impediment to grazing. We now have about five 7ha blocks.”
He has kept his calving block fenced normally to help keep calves in.
Fraser says the cows ignore him now when he goes to check on them in the paddock. That makes it easier to check dry mobs because they don’t make a mess wanting to be shifted when they see him.
“I think it’s actually calmed the cows down more. You can walk around the paddock checking the cows and they are not worried about you.
“I find I actually go to the cows more because I can walk around the paddock without upsetting them.”
The time and labour saved and the stress the technology takes away has potential to help farmer’s mental wellbeing, Fraser says.
“I don’t have to get up early to get the cows in, I schedule what time I want them at the shed and they meet me there at 5.30am every morning. It’s quite a big thing getting that sleep back.”
He simply schedules what time he wants the cows to arrive at the farm dairy, the collars start vibrating to move the cows toward the shed and they get to walk at their own pace.
PASTURE ALLOCATION
Fraser does a farm walk every three weeks, and will do it more frequently in spring. He then loads that information into the Halter app to work out a precise pasture allocation.
In the app he then draws the break for the cows of where the virtual fence boundaries will be. The app shows kg DM/cow, square metres/cow and also total area.
“It calculates how much grass down to a decimal point. We’ve always farmed on averages. We don’t have to anymore, we can be precise.
“You can fence and manage your pasture in a new way. The breaks don’t have to just be half a paddock or a third of the paddock.”
The break can be any shape, it can be drawn around areas to avoid in a paddock, such as wet areas in winter. Back fencing is also simple, meaning the pasture is not being regrazed and is growing the next day.
In summer, Fraser drew breaks that would push the cows toward shade during the hottest part of the day to stop them overgrazing.
He has always wanted to run the cows in two herds to give more options later in the season, but it was too difficult on his own.
Peter still rears the calves, and typically they have employed extra labour until during spring. This year, Fraser will not need to employ any staff.
He is now running two herds,120 of the younger and lighter animals, and 180 of the mixed-age cows in the other mob.
SHIFT TO TWO HERDS
Running two herds enabled him to put the younger or low performing cows on once a day (OAD) earlier this season and carry on milking the older cows that were still producing well twice a day for longer.
“The cows have always had to be on the same milking frequency. Now I can milk the well producing girls longer into the season – that’s been really big for us.”
As a result, they’ve had a record season this year, although the season has also been particularly helpful with a good summer and autumn.
The beauty of the smart collars is he can run as many mobs as he wants. So for cavling, he can have a dry mob, a springer mob, colostrum cows and the milkers. They will all get shifted on a schedule, meaning he doesn’t need any help drafting them or getting them to and from the farm dairy.
Drafting springing cows this calving will be walking around the paddock looking for cows who are bagging up, and using the app, allowing them to walk through to fresh grass by giving them a new virtual boundary.
The other plus is being able to have the data records for any compliance regulation, Fraser says.
They can print reports on where the cows have been, down to a heat map which shows where the cows ‘camp’ in paddocks. They can put that data into even more precise nutrient application.
The technology is not just an incremental change it’s flipping the whole industry, Halter business development manager Steve Crowhurst says.
Cows have traditional cues of farmers, gates, dogs, motorbikes, to tell them it’s time to move.
“We’ve repackaged those cues into the collar. We retrain the cows to respond to the sound and vibration.”
The solar panels on the collars mean the batteries are constantly charged and working 24/7 and the collars are taking 3000 readings per minute from each cow, measuring 22 different behaviours, from walking, sitting to grazing.
This data is then put through algorithms to determine if a cow is behaving differently, which sends health and heat detection alerts to the farmer.
“The collars are saving a 400-cow farm 20+ hours of labour a week,” Steve says.
Halter owns and maintains the collars and farmers pay a subscription fee per cow/month.
FARM FACTS
Owners: Peter and Sue Hasnip
Manager: Fraser Hasnip
Location: Pirongia, Waikato
Area: 106ha effective
Cows: 300 Friesian crossbreds
Mating: 11 weeks Artificial Breeding (no bulls)
Production: 127,000kg MS
Pasture & Crop eaten: 15.5t DM
Supplement: 0.5t/cow/year (70% palm kernel, 30% DDG blend)
Crops: 5ha maize, 6ha turnips
Effluent irrigation: 25ha