Overcoming AB hazards
The efforts farmers have put into making their artificial breeding (AB) facilities safer for technicians has had a dramatic effect on reducing injuries, reports Anne Lee.
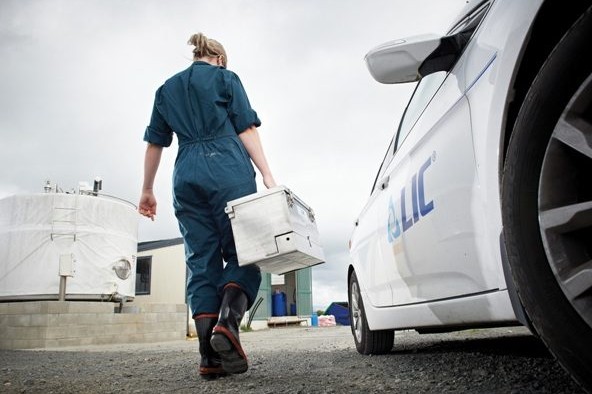
Total reportable incidents from LIC’s AB technician group for the 2018 season, ending May 31 this year, plummeted by 47% compared to 2017 season and were down by 43% compared to 2016.
It’s too soon to collate the information yet on how this season’s mating has gone but LIC national AB manager David Hale says he expects farmers’ continued endeavours and investments will have an ongoing and lasting positive impact on the co-op’s 840-plus technicians with fewer of them coming to harm while going about their work.
Injury rates among AB techs had been far too high, he says.
‘When we went out to farmers with this initially, we pushed for it on the basis that better facilities would give our technicians a better chance of getting cows in-calf as well as making it safer for them to work.’
Slips, trips and falls were the most common cause of harm and while that sounds like the injuries are more likely to be minor, many were not.
Broken legs, arms and elbows, dislocated limbs and even concussion were all too common as a result of techs battling with second-rate trolleys or even balancing precariously on a couple of planks of 6×2.
“By and large rotary shed AB facilities are very good although some of the very old models needed a bit of work, but it was far too common for our people to get hurt in herringbone set-ups that were just unacceptable and mostly avoidable.
“They’re either using an unsuitable trolley or standing on some kind of home-made platform – that could be made from just about anything you can imagine – planks of wood laid across a couple of sawhorses even.
“What we’d ultimately like to see is AB being moved into separate purpose-built AB and vet facilities off to the side in the yard.
“There are just so many hazards in a herringbone (farm dairy) – the AB tech is often having to drag themselves along the row on the AB trolley, they’ve got hoses and lines to contend with and vertical steel poles.
“If a cow moves while they’re inseminating it close to those poles you’ve got a big risk of their arm being jammed up against them.”
David says farmers were told early last year that a national standard for AB facilities would be implemented before mating 2018 and what was necessary to meet the standards.
“We went to farmers early to give them plenty of time to make changes and upgrade facilities where needed.”
Three standards were set – bronze, silver and gold with farm facilities having to meet the bronze standard to be compliant.
If they didn’t meet that bronze standard the message was clear – LIC would not be providing an AB tech service.
CRV was on the same page so farmers knew it wasn’t simply a matter of switching companies.
Thirty of LIC’s technicians were selected and trained in assessing facilities against the national standards.
David says there was reluctance from some farmers and many of those who needed to upgrade to be compliant left their run very late.
“When we went out to farmers with this initially, we pushed for it because better facilities would give our technicians a better chance of getting cows in-calf as well as making it safer for them to work.
“There were some who weren’t happy because they couldn’t see why they had to change what they’d been doing for years.
“We had just over 1000 facilities that weren’t compliant with the bronze standard on the first check but in the end, we only had one farm where it came down to having to send a formal letter of notice that we wouldn’t AB in their facilities unless they were upgraded.”
All up they currently have 8398 inspected and compliant facilities with more than half of those at a bronze standard.
Most of the gold standard facilities are in the South Island and a large proportion of those are in Canterbury where the farm dairies are typically rotary and have been built in the last 20 years.
David believes they got better momentum approaching it from the point of view of improving the working environment to enable the best chance of getting cows in calf at first presentation than would have come from going down a straight health and safety track.
People need to be presented with the benefits because they often see the words health and safety and think of it purely as compliance and a cost, he says.
“But every single farmer I’ve spoken to who has upgraded from ABing in the herringbone to having a standalone purpose built facility has said they should have done it years ago.”
They’re multi-purpose so they get used by the vet for animal treatments, Tb testing, the list goes on, he says.
LIC staff have connected with farm dairy builders in several regions where herringbone farm dairies are being built, most commonly where farms are being amalgamated or reconfigured and essentially re-converted.
“As soon as we know that’s happening, we’re suggesting putting in the purpose-built handling facility because it’s not a lot of extra cost relative to the overall cost of that development and we’d really like to see people getting right out of ABing in the herringbone.”
David says the assessment of facilities isn’t a one-time thing largely due to a somewhat impractical tradition where the sharemilkers often own the trolleys or platforms used for AB.
“That means they’re not necessarily a good fit for the shed they move to so we’re having to go and do inspections when a sharemilker moves after gypsy day.
“That can be more than 2000 re-checks.”
Yearling AB facilities too caused a few headaches with graziers sometimes not happy with having to upgrade.
“We left dairy farmers to sort that out with their graziers themselves, but the rules were adhered to just the same – if they didn’t at least meet a bronze standard we weren’t going in to AB.”
It wasn’t just the farmers having to make changes though.
David says some of the technicians who have been doing the job for many years had to adjust their thinking too.
They’re no longer allowed to be in the same space as the cows.
They must be protected by a barrier.
“It wasn’t uncommon for some of our technicians to arrive onfarm and have the cows waiting in the yard or holding paddock and for them to have to help get them in and row up the cows either helping the farmer or in some cases by themselves.
“Some of them have been doing it for years or have been standing on pretty sub-standard, unsafe platforms and just went with the flow.”
While 10-15 years ago almost all AB technicians were or had worked on dairy farms as a job now only around half would be dairy farmers.
“We have police, firefighters, nurses and people from all sorts of careers and backgrounds who take four to six weeks off to do an AB run.
While the majority of technicians being trained in recent years have been women, the overall gender makeup of the team is 43% women, 57% men.
The push now is to get farmers who just make the grade and are at bronze level to make changes so more facilities meet silver and gold standards.
“The more safely and efficiently AB techs can do their jobs the more productive it is for farmers and technicians, getting more cows in calf the first time they are presented and operating in safe work environment.
“No one wants to see people getting hurt and I don’t think there’s anyone out there who wouldn’t think that’s fair enough.”