The effluent efficiency experts
Size does matter. Mike Visser talked to Sheryl Haitana about how well designed infrastructure is making easy work of the farm’s effluent several years after it was built.

From the natural gravity fall to the capacity and shape of the sludge beds, a Te Awamutu dairy farm is benefiting from a sophisticated effluent system design.
Haerepo Trust Farm at Te Awamutu has no expensive solids separator or vibrating screens, just separation mesh screens the effluent filters through, which is so efficient there is no stirrer required in the pond.
It’s a design which has taken away the headache of dealing with effluent on a daily basis, sharemilker Mike Visser says.
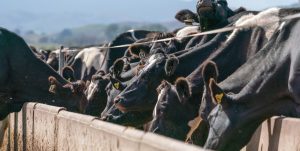
“It’s really turned a liability into a huge asset.
“We are fortunate here that it is all natural fall, so there is no pumping at all to get from the feedpad to the pond. It’s all gravity though the sludge beds into the pond.”
The only pumping required is from the pond to the Weta low-rate irrigator and the flood wash tank.
“We are not reliant on power to get the effluent into the pond so if there is a power cut we don’t get caught out. And we don’t get the wear and tear on pump gear.
“Because anything that has to deal with effluent needs a high level of maintenance. Effluent is very corrosive, it’s horrible stuff.”
MIke and Sue Visser have been sharemilking for the Barton family between Te Awamutu and Otorohanga since 1997. The position was originally 170ha milking 550 cows, but grew in 2001 when the family purchased 120ha across the road. They now are milking 950 Friesian and Friesian crossbreds in a split calving system, milking 200 cows through winter.
The farm’s original effluent system consisted of a feedpad which they scraped daily into a tiny pond at the bottom of the feedpad. That pond only had about four days worth of storage, half of that storage was taken up by the solid crust on the top, Mike says.
The pond had to be daily stirred by a tractor power take-off stub shaft and the irrigation lines were constantly blocked or the flow was so low the travelling irrigators hardly worked.
It was a daily stress trying to spread effluent in ideal conditions and meet regulation in ideal irrigation weather, let alone in high-risk weather.
“I think we did exceptionally well with what we had to work with, but looking back the risk was pretty high,” Mike says.
The farm is predominantly Mairoa Ash soil with some Punui silt loam soil on the river flats next to the Waikeria Stream, which borders part of the farm.
Running an intensive DairyNZ system 3-4 split calving operation on high risk soils, they needed a better system to mitigate risk and turned to Agfirst engineering consultant Davieth Verheij to design a solution.
The new effluent design involved slightly extending the feed pad and building a concrete gutter at the end, falling from 500mm to 2m deep. There are two green water jets at the bottom of the gutter to help solids move along.
They installed a green water floodwash, which does not reach the entire feed pad so they still have to scrap the corners with a scraper on the back of a quad bike. But that is only a quick 10 minute job, Mike says.
From the gutter the effluent flows into two sludge beds, each 76m x 8m. The beds have no vibrating screens, just two AgFirst segregation screens which don’t need to be cleaned. The screens achieve a three stage filtration process through each sludge bed which catches the finer fibre.
This system prevents the effluent solids being forced to the end, blocking the weeping wall up, which you often see happening on other farms, Mike says.
“Our sludge beds are fantastic, the size does matter apparently and that’s where a lot of them go wrong. It’s all to do with hydraulic power from one end to the other, and it’s your ratio of length to width. A lot of square sludge beds don’t work.”
FILTERING THE LIQUID
The end result is more liquid can filter through and the solids remaining are drier, giving another three months of additional solids storage in the sludge beds.
“The pond does not require a stirrer because the size of any particles that can get through the Agfirst three stage weeping wall system should be small enough that they stay suspended.”
The pond is 8m cubic litres which gives them months of storage over winter and spring and a great irrigation asset to use in summer. They irrigate over 55-60ha using a Weta travelling rain gun, which automatically shuts down if there is no pressure or low pressure.
“This makes the system a lot safer – a lot more manageable.”
The sludge beds are cleaned out every six months with a digger, once in spring and the next one then in autumn. Because of the filtration system they are left with very dry solids, making it easier for the digger to clean out as it’s not slop. It is spread onto the maize paddocks and down the sidlings.
They grow 25ha of maize onfarm each year, rotating the crop around the poorest performing paddocks. They plant via strip tillage which suits the fragile soils instead of full cultivation.
Using effluent on those maize paddocks generally means they don’t have to use synthetic fertilisers, Mike says.
However, they soil test biannually and test their effluent to ensure the balance is right.
“We wanted to quantify what was in the sludge so we had it tested, which was an eye opener. Because the potash stays with the water, it means there was very little K (potassium) left in the solids, so it meant the sludge wasn’t an ideal maize fertiliser on its own.”
They use a DAP or MOP fertiliser mix and 140-150kg N/year over the rest of the milking platform.
They also buy in another 17ha of maize silage, 350-400t palm kernel and hay for the winter which is all fed out on the feed pad.
They feed all supplements on the feed pad, which has a 400-cow capacity, eight months of the year. Not having to feed out in the paddock prevents a lot of wear and tear on machinery and avoids tractor error on some of the hillier terrain, Mike says.
The farm is 80% flat to easy rolling country, with 20% of medium rolling land. There are a few steep sidlings that are not part of the milking platform.
They harvest about 13t DM/ha pasture in a good year, Mike says.
“One thing we’ve found that works really well for us is to plant ryegrass with no clover in it. “That means we can use a strong weed killer without having to protect the clover and then we oversow the clover the following autumn.”
They winter milk 200 cows and graze 200 cows off farm in the winter for six weeks, with the remainder staying onfarm.
The cows are generally run in three herds, with a herd of heifers and young and lighter cows, a herd with the bigger Friesians and the other herd with the smaller Freisian/crossbred cows.
LEAPS AND BOUNDS
The maximum walk to the farm dairy from any direction is 2km. The farm as it is today was amalgamated from three smaller dairy farms and each farm still has its own dosatron and electric fence unit.
Mike still runs it like three farms, with a herd manager each looking after one herd and essentially their own farm. That sets them up to take on a farm manager role because they are looking after everything, from the cows to the water on their block, he says.
“It’s a great training position so it’s not such a big jump up to farm manager.”
Staff share every job onfarm from milking to the tractor work, because it gives variety in their job and they are all important skills to have, he says.
Mike and Sue won Waikato Sharemilker of the Year in the 2005 Dairy Industry Awards. When Mike looks back now they were doing a good job onfarm when they won the sharemilker of the year, but they were doing a lot of cultivating, using a lot of synthetic fertiliser, and poorly utilising effluent. “We have come along leaps and bounds, in our understanding and our practices and use of technology. I think that is true of a lot of farms.”
They have chosen to keep their sharemilking job and invest off farm.
“We are very fortunate to have a great relationship with the owners, and we treat this farm like our own.”
They had a share in an equity partnership dairy farm which they have since sold and bought 12ha of hops in Nelson.